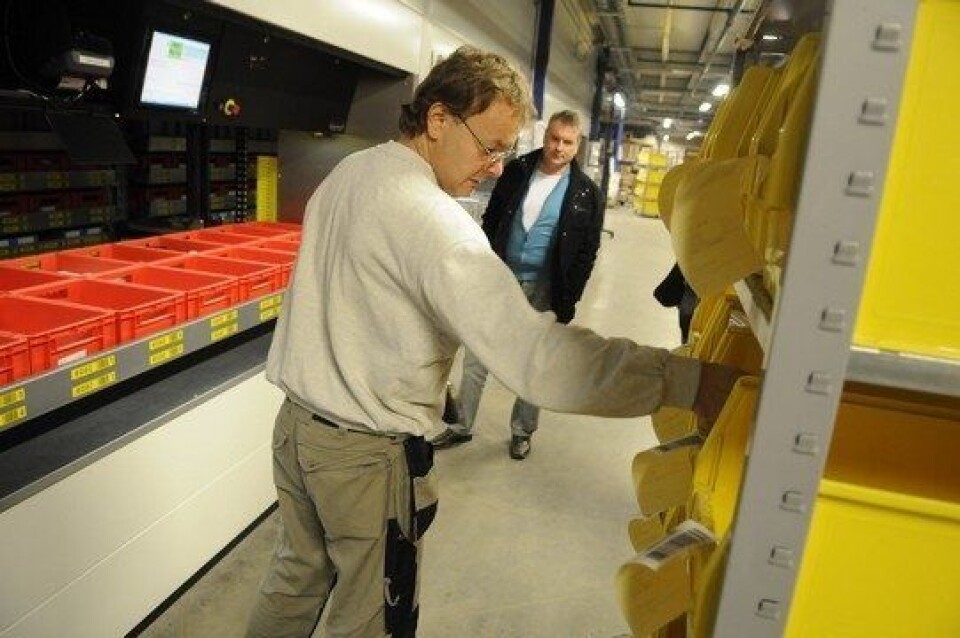
Mindre lager, men økt kapasitet i Moss
MOSS: Handicare AS har spesialisert seg på salg og service av tekniske hjelpemidler til eldre og funksjonshemmede. Produktområdet er bredt og tilpasset både barn, unge og voksne. Sortimentet baseres på egenproduserte produkter og agenturprodukter fra anerkjente leverandører, for å gi brukerne en enklere hverdag. Nå har bedriften selv fått en hjelpende hånd på lageret.
Merk at denne artikkelen er over ett år gammel, og kan inneholde utdatert informasjon.
- Vi gikk fra et lager på 4000 m2 til 1500 m2. Likevel får vi unna mer enn tidligere, sier Thomas Trier, Logistics manager i Handicare AS. Handicare har nemlig også fått inn lagerdriften til datterselskapet Puls AS, som styrer forretningsområdet som inkluderer medisinteknisk utstyr og forbruksmateriell, under samme tak.
Trier forteller at prosessen ble satt i gang i mars 2009 for bedriften som har satt seg som mål å gjøre hverdagen enklere for pleietrengende, pårørende og helsepersonell. Gamle og uhensiktsmessige lokaler i Moss er nå byttet ut med mer moderne lokaler i samme by, og inneholder både administrasjonslokaler, produksjon og lager.
Lager og Industrisystemer
Det første Handicare gjorde var å se nærmere på godsstrømmen og hva slags gods som håndteres på lageret.
- For oss var prosessflyt et nøkkelord i den innledende fasen, forteller Trier.
Lager og Industrisystemer AS var inne fra første stund, først i forbindelse med forprosjektet, og lagerspesialisten fra Vinterbro vant også anbudet da planene skulle realiseres. – LIS vant ikke fordi det var de som tegnet for oss, det var fordi de var konkurransedyktig på pris og fordi de hadde gode løsninger, forteller Trier.
Ny hverdag
Da Handicare tok i bruk det nye lageret rundt 15. februar var det en helt ny hverdag sammenlignet med tidligere. Manuelle plukklister, penn og papir er nå byttet ut med PDA’er, headset og strekkodescannere.
- Å følge en vare med en strekkode var en ny hverdag for oss. For ikke å snakke om inngående varestrøm der vi tidligere “fant en ledig plass” og skrev ned hvor vi la varen. Nå styres alt av WMS, forteller Trier.
- WMS gir oss den informasjonen vi trenger for å sikre effektiv lagerdrift. I tillegg til å styre produksjonen gir den også oversikt over eventuelle flaskehalser og kan styre ressursene dit det er behov for det. Gjennom WMS får vi også statistikk for å måle effektiviteten og forbedringsområder, forteller Trier.
Lagerautomater
Totalt innredet LIS ca. 1500 m2 høylager (10 meter fri høyde). Dette inkluderer blant annet fem Logimat-lagerautomater på ti meter som er forbeholdt småvarer.
- Mellom 60% og 70% av plukket vårt er fra automatene, sier Trier. Gjennom noen få tastetrykk på PC’en viser han frem statistikken som indikerer at automatene nesten er fylt til randen.
- Akkurat nå har de en fyllingsgrad på 97%, mens totalen for hele lageret vårt er 73%, forteller han.
Lagerautomatene er forbeholdt høyfrekvente småvarer. Lavfrekvente småvarer er henvist til mesanin på 400 m2 som ligger over plukksonen.
- Gjennom å utnytte arealet over plukkområdet (mesanin) får vi en svært god utnyttelse av gulvarealet vi har til rådighet. Det vi gjør er jo å utnytte en “død plass”, sier Trier.
Shark WMS
Hjernen på lageret er lagerstyringsprogrammet Shark WMS (Warehouse Management System). Softwaren er integrert med Handicares ERP-system (Axapta), og gir en oversikt over “ståa” på lageret.
Det er Shark WMS som tildeler en inngående vare til en av de 14.000 lagerlokasjonene, basert på godsets størrelse/mål og plukkfrekvens. Det er også Shark WMS som styrer ordreproduksjonen. For de høyfrekvente varene går det i batchplukk der plukkerne plukker til 16 ordre av gangen.
Lagermedarbeider Morten Hansen ga oss en rask omvisning i rutinene. Etter å ha hentet opp en ordreliste fra Shark WMS triller han frem en vogn med 16 bokser, en for hver ordre. Først plukker han fra gjennomløpsreolene på sin venstre side. Monitorer forteller hvilke hyller han skal plukke fra, hvor mange kolli han skal plukke, og hvilken av de 16 kassene han skal plukke til.
Når han er kommet til veis ende for gjennomløpsreolene foretar han en u-sving og befinner seg foran den første heisautomaten. En hendig og informativ monitor gir ham rask oversikt over hva som skal plukkes, og lysdioder viser hvilken boks i automaten han skal plukke fra.
Økt effektivitet og nøyaktighet
- Etter at vi fikk nytt lager og nye lagerløsninger har effektiviteten økt betraktelig. Gjennom samlokalisering (Puls og Handicare under samme tak) og effektiviseringsverktøy, har antallet lageransatte blitt redusert fra 13 til 10. I dag har vi plukkere som plukker over 700 ordrelinjer på en dag, en klar forbedring fra hvordan det var tidligere. Dessuten har nøyaktigheten økt. Ettersom plukkeren også har et kontrollsiffer etter plukk kan man nesten ikke plukke feil, selv om man skulle gå inn for det, sier Trier og smiler.
Printer i trucken
I tillegg til konvensjonelle pallreoler har Handicare mobile pallreoler for bufferlager og plukk av lavfrekvente varer. Reolene er inndelt i soner i forhold til hvilken trucktype som betjener sonen. En skyvemasttruck betjener bufferpaller i område 8-10 meter i tillegg til helpallsplukk, innlegg og tompallshenting, mens to plukktrucker betjener området fra 8 meter og ned til 2. bærejernsnivå med kolliplukk fra pall. Gulvnivå betjenes av ledestablere.
Vi ble med truckfører Morgan Angeland rundt på en plukkrunde. Løypa er forhåndsbestemt av Shark WMS, og Angeland vil hele tiden kjøre i «riktig kjøreretning». Skyvemasttrucken hans er den eneste av truckene som foreløpig benytter «Pick-by-voice». Angeland ledes til riktig plukkgang og riktig høyde av en myndig kvinnestemme på øret. Når han ankommer lokasjonen får han beskjed om hvor mange kolli som skal plukkes (evt. hvor mange kolli som skal etterfylles).
- Jeg jobber mer effektivt nå enn tidligere, sier han.
Trucken er også utstyrt med printer som skriver ut både transportetiketter (SSCC nivå 3) som inneholder sendingsnummer (fullt ut integrert med Consignor) og kollietikett som forteller kunden hvilke artikler og mengde som ligger i et hvert kolli.
Få barnesykdommer
En så stor omlegging av rutiner og løsninger forløper sjelden helt knirkefritt.
- Hos oss gikk det egentlig veldig bra. Noen utfordringer var det i oppstartfasen, men ved hjelp av ekstra ressurser klarte vi oss bra. Vi hadde ikke driftsstans og kundene fikk varene sine, forteller Trier.