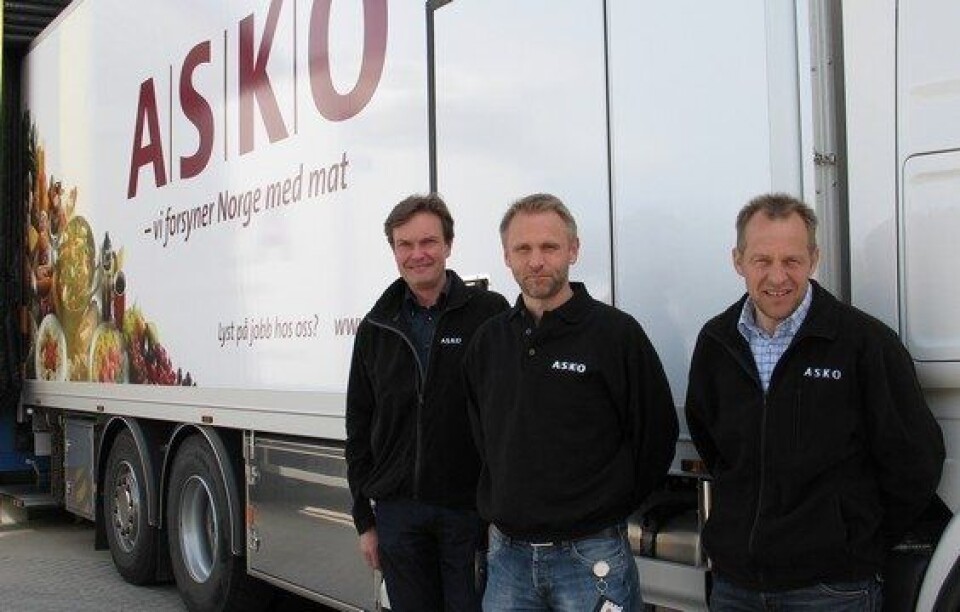
Reduserte feilplukk med 90%
BRUMUNDDAL: ASKO Hedmark på Brumunddal har redusert feilplukk med 90% etter at man har gått over til stemmebasert plukk på lageret.
Merk at denne artikkelen er over ett år gammel, og kan inneholde utdatert informasjon.
Ved plukk basert på stemmestyring får plukkeren all informasjon rett inn i øret og må fortløpende kvittere for det han/hun gjør. Vi fulgte lagermedarbeider Geir Egil Mikkelsen en kort runde på kjølelageret da han skulle plukke en pall til en kunde. Mikkelsen fikk hele tiden beskjed på øret hvilken neste vare han skulle hente, og han måtte hele veien bekrefte før han kunne fortsette videre. Alt som plukkes sammen for uttransport, står på gulvnivå og er lett å nå. Mikkelsen er godt fornøyd med systemet.
– Dette er et fantastisk hjelpemiddel til å få gjort jobben riktig og raskt, sier han, før han haster videre.
21 mill. kolli
ASKO Hedmark på Brumunddal jager konstant kvalitet og effektivitet og tar mål av seg å være Norges mest kundeorienterte og råeste logistikkmaskin. Årlig sendes 21 millioner kolli, som representerer 230.000 m3 varer, ut til 1.300 kunder i Hedmark og Oppland.
Av dagligvarebutikkenes innkjøpsvolum leveres rundt 70% av grossistene, og andelen er økende. ASKO legger ikke skjul på at de har ambisjon om å bli 100% leverandør til sine kunder.
- Det er tre varestrømmer innenfor systemet vårt. Noe går direkte fra leverandør til sluttkunde. Typiske eksempler på det er varer fra Tine og Ringnes. Noe går direkte fra leverandør og hit for lagring. Den siste varestrømmen er transitt, hvor varene kommer kundepakket til vårt anlegg for sammenstilling med resten av leveransen til kunde. Alt er lagt opp for at vi skal kjøre mest mulig fulle biler. Mesteparten av inntransporten hit utføres av eksterne transportører, og også her er fulle biler og effektiv transport alfa og omega, sier Geir H. Halvorsen, som er ansvarlig for inngående gods.
Elektronikken styrer
- For kundene er det stort sett to ting som teller, at varene kommer til avtalt tid og at de får det de har bestilt. Dette styrer i realiteten all virksomheten vår, sier Myrbekk. Han er ansvarlig for logistikken når varene er ferdig kontrollert og tilgjengelige for plukk.
- Vi har i størst mulig grad forlatt papiret. Alt styres elektronisk. Vi har et logistikkstyresystem som heter IMI. Kort fortalt holder systemet kontroll på hver eneste vare gjennom hele varestrømmen, forklarer Myrbekk.
Fulle biler ut
ASKO Hedmark har 28 egne distribusjonsbiler pluss 12 biler i isdistribusjon for Hennig Olsen. Opptil 35 ruter går ut fra anlegget i Brumunddal hver dag. Noe går på leietransport. Bilene kjøpes på rammeavtale med Scania og har 3-temperaturs skap fra SKAB.
– Vi har et egenutviklet flåtestyringssystem som heter TOS, sier Myrbekk. – Noe av det viktigste med dette systemet er at det styrer varevolumene og setter sammen mest mulig fulle lass. Derfor kan det godt hende at en butikk får en av pallene sine med en annen bil enn den som leverer resten. Sjåførene er selvsagt en viktig brikke i systemet. De skanner alle varene inn på bilene, noe som sikrer at alt kommer med. Etter hvert vil de også skanne leveransene av bil ute hos kunde. Vi har full logging av alt som har med temperatur å gjøre og det meste ellers på bilene, forteller Myrbekk.
Miljøet i fokus
Miljøet står i fokus hos ASKO, som har ambisjon om å være klimanøytral innen 2020.
– På noen biler har vi CO2 som kjølemedium. Det er ekstra miljøvennlig, både fordi vi benytter CO2 som ellers ville gå ut i atmosfæren og fordi vi slipper dieseldrevne aggregater. ASKO har klare miljømål. Innen 2012 skal energiforbruket reduseres med 10%, CO2-utsllippene med 40% og 85% av avfallet vårt skal kildesorteres, sier daglig leder Terje Flaatrud.